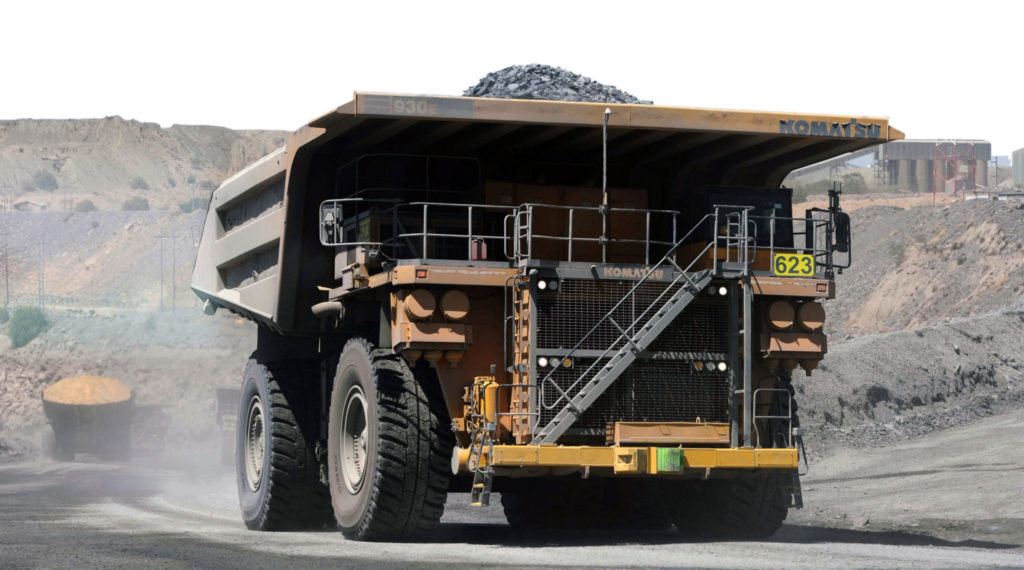
A haul truck is pictured at the Jwaneng mine of Debswana, the world’s leading producer of diamonds by value in Botswana, on October 4, 2016 in Jwaneng. / AFP PHOTO / MONIRUL BHUIYAN
In the face of increasing automation, Africa’s resource economies will not have the time to create an industrial middle class as developed nations did
The effect of increasing mechanisation on the industrial sector has been a hot topic in the developed world as displacements in the labour market, due to automation, have led to polarisations in economic inequality and even political blowback through a rise in populism. The rise of automation has been a long-term trend, with the pace of increasing mechanisation made viable through the cost benefits of cheaper, more efficient robots relative to higher-wage workers. There has been a general move to capital over labour.
Internationally, the effects that industrial automation will have on resource economies in Africa have not received as much attention. However, a 2016 World Bank study focused on the potential influence this trend might have on these developing nations. Overall, the World Bank study was inconclusive: many of these economies have yet to reach the wage pressures cited above to make widespread automation attractive.
But a 2016 Citi GPS report, based on the World Bank data and co-produced with the Oxford Martin School, has shown that developing countries face a higher future risk that includes the current displacement of labour and a lack of need for future labour due to mechanisation. Building upon previous work at the Martin School, the report found that 69% of jobs in the developing world risk being replaced through automation as opposed to 47% in the US, for example.
Many of Africa’s established and emerging industrial leaders are high on this list, with estimates of 65%, 67%, and 85% (the highest measured in the study) for Nigeria, South Africa, and Ethiopia respectively. Lower wages may delay this process, but it has already begun in some sectors in Africa.
The mining industry is prolifically present throughout the continent. Mining is also a labour-intensive industry where the work is often codified and repetitive, making it an exceptionally attractive candidate for mechanisation. In South Africa, this is combined with relatively high wages, making the country’s mining sector a predictive case study of the effects this process might have on other African economies in future.
In September 2016, a South African Chamber of Mines report was candid: modernise or risk slow extinction over the next two decades. In February 2017, the chamber’s vice-president, Neal Froneman, told businesslive.co.za, a South African news outlet, that South Africa’s mining industry faced steep production shortfalls and job losses if it did not switch to the new, smart machines. As it is, the South African mining industry shed 59,407 jobs between 2012 and 2015. The Chamber of Mines says another 200,000 jobs are at stake in the gold mining sector alone.
Mechanisation is “radically” changing South African mining, said Froneman. If implemented effectively, with 24/7 operations, mechanisation could maintain current output beyond 2030. This would directly buoy the 7.7% of the total South African GDP derived from mining. The knock-on effects could be even greater, given the number of local industries and communities that depend on the sector to provide product demand and disposable income, respectively. Some 500,000 jobs and five million people fell into these two contingent categories in 2007.
When framed as an existential dilemma, the move to mechanisation in South Africa echoes the discourse in developed economies over recent decades. After all, saving some jobs is better than losing them all. But does it also portend the same working class backlash that has taken place in some of those developed economies?
Of course, mechanisation offers the mining industry a major opportunity to realign its labour commitments. In South Africa, a main turning point toward mechanisation took place in 2014. After several years of labour disputes and strikes – along with a violent struggle between the Association of Mineworkers and Construction Union (AMCU) and the National Union of Mineworkers (NUM) over membership – platinum producers in the country united in making large capital investments in mechanisation.
In the same year, both unions wrestled with the effects that mechanisation might have on their members. Frans Baleni, who was then NUM’s general secretary, said his union had “a problem” with the introduction of mechanisation “if its sole purpose is to replace labour”. If the changes were “about safety and the workers getting more pay”, however, the union wouldn’t “have such a problem”.
At the time, many in the ruling African National Congress (ANC) advocated Baleni’s view; mechanisation might move the industry away from dangerous labour-intensive production toward the government’s goal of “zero harm”.
So far, the ANC has walked a fine line between corporate and labour interests in the sector by stressing higher wages and the safety advantages of mechanisation. Ostensibly, this makes sense for the South African economy as a whole. Yet the argument sounds much like the justifications that have been used in developed economies. So, if Africa is following the same pattern, it should heed the lessons from the past few decades to avoid the pitfalls experienced elsewhere.
Indeed, learning these lessons might be even more critical for Africa. Dani Rodrik, a political economist at Harvard, said in a 2016 article on “premature deindustrialisation” that increasingly better labour-replacing technology would lead to fewer future industrialisation opportunities for developing economies. This means that Africa may not effectively capitalise on a sector that was critical in creating the middle class in the developed world during the last century.
Indeed, manufacturing output in sub-Saharan Africa, as a percentage of GDP, is lower today than it was in 1980. Coupled with the relatively high potential for vulnerability in the African economies cited above, this means that African nations will have to be more nimble in retraining their labour forces if they are to continue emerging economically.
Mechanisation is already underway in some South African mining operations. At South Deep, in Gauteng province, drill-rig operators are replacing labour-intensive rock drillers. Some of these new positions offer much higher wages, about $5,000 per month as of 2014. But there is a caveat; the company also hired a team of Australians acquainted with mechanisation techniques to help meet production goals.
By mechanising resource extraction, Africa invites further inflows of foreign workers more experienced with the machinery. The current labour force will need to be retrained, quickly and holistically, to deal with the duel pressures of mechanisation and global labour pools. In the extractive industries generally, this means making the step from manual labour to operator – which, to a degree, is already underway for the mining industry.
People whose jobs aren’t saved will need retraining for entirely different industries. Failure to manage this will see middle-skilled workers falling down the economic chain, where they will compete with lower-skilled workers, further polarising economic inequality – as has happened in many developed economies.
A February 2017 Knowledge, Evidence and Learning for Development (K4D) report, published by the Institute of Development Studies in the UK, stresses the importance of education that imparts transferable skills to new and existing workers. This would facilitate a labour transition from codified and routine work that has been automated to “higher paid, non-routine jobs” that are resistant to mechanisation. This approach not only blunts the effect of mechanisation on domestic employment, but also seizes an opportunity to diversify worker skills by making them more globally competitive.
African economies have an additional opportunity, due to generally lower wage structures vis a vis developed nations. This will give them a competitive cost advantage, since many of these types of jobs are globally sourced.
Additionally, retraining workers for new, flexible non-routine jobs will help make extractive economies more resilient through diversification. Such an approach should also not be limited to current workers; it should include the next generation, for which even fewer extraction jobs will be available. The K4D report cites some low-cost initiatives, such as the Bridge Academies in Kenya, as a possible successful format.
Some developed nations avoided an honest conversation with their labour forces as mechanisation took hold. African nations will need to heed this lesson. Mechanisation might save the mining sector in places like South Africa, as it did with the auto industry in the USA, but it won’t preserve the levels of employment seen in the past. This fact could be negative or positive, depending on how soon it is addressed.
Africa’s raw deal is that the continent’s emerging economies never had the time to create an industrial middle class, as developed nations did. The upside is that Africa can learn from the mistakes of economies that depended too greatly on those industries. Its best competitive advantage in the more flexible professions of the future could be its youth and wage advantage – if the proper steps are taken now.